RHODaS partner the Austrian Institute of Technology has published a report entitled "Power converter design, modelling and simulation" to present their work carried out on the design and validation of a high-power inverter for heavy-duty electric transport. The report aims to provide a comprehensive understanding of the design process, the different components of the inverter, and the control strategies employed.
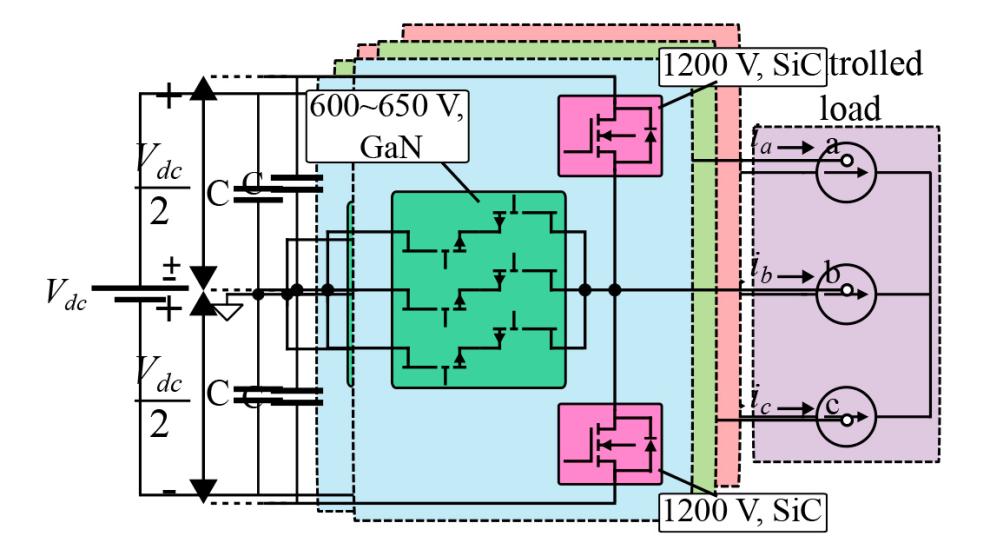
The report details the intricate process of constructing the inverter, spotlighting key components such as the heatsink and the main power board with GaN power semiconductors. The heatsink is designed with specific dimensions and interfaces to ensure efficient cooling of the semiconductors. The main power board consists of GaN power semiconductors, drivers, optical interfaces, and DC link capacitors. The report also discusses the decision to exclude a DC-DC converter in the design, citing higher battery voltages, simplicity, cost optimisation, and environmental benefits as the principal reasons.
In addition to its focus on design and construction, the report examines control strategies pivotal in maximising the T-type inverter's performance. Employing Piecewise Linear Electrical Circuit Simulation (PLECS), it compares the efficiency of various modulation strategies, aiming to pinpoint the most efficient approach while minimising switching losses, and analyses the DC-Bus balancing.The intricacies of the inverter control platform are also detailed, dissecting both its hardware and software components. By delineating the architecture and functionality of the control platform, the report underscores the indispensable role of robust and efficient control systems in enhancing overall inverter performance. Through meticulous validation and analysis, the report not only scrutinises the design's efficacy but also offers valuable insights into its strengths and limitations.
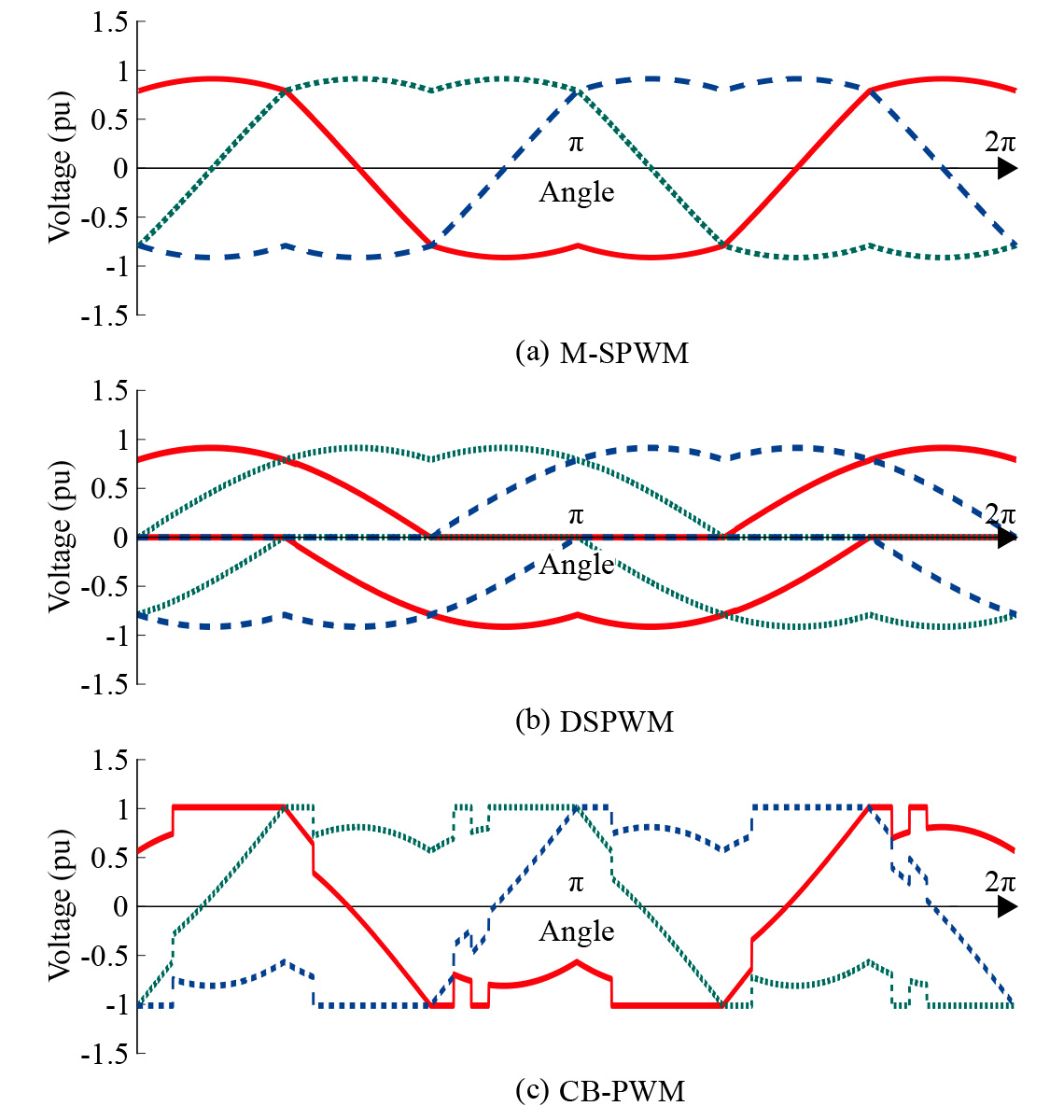
The validation of the hybrid inverter design is presented based on a low-power inverter model. The working principle of the T-type topology is explained, along with the current commutation during switching. PLECS simulations are conducted to assess the switching losses, and a double pulse test is performed to analyse the switching behaviour.
Overall, the report provides valuable insights into the design, modelling, and simulation of a high-power inverter for heavy-duty electric transport within the RHODaS project. The detailed analysis of the different components, modulation strategies, and validation results demonstrates the thoroughness of the research and development process.The main conclusions reached, and results obtained were, firstly, the successful implementation of the high-power inverter's design and construction, accentuating key choices such as the omission of a DC-DC converter. Justifications for these decisions extend beyond technicalities, emphasising higher battery voltages, simplicity, cost optimisation, and environmental benefits, underscoring the holistic approach towards efficient power conversion used within the RHODaS project.
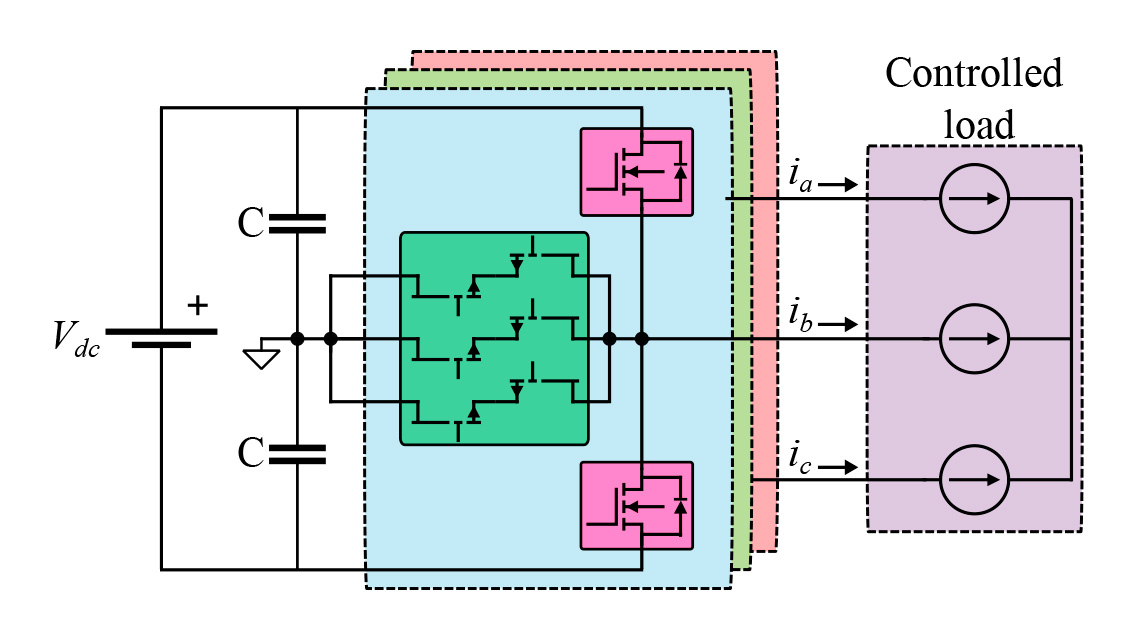
Secondly, the report details the effectiveness of specific modulation strategies utilised in controlling the T-type inverter, crucial for optimising performance, specifically, the delicate balance between minimising switching losses and maximising overall efficiency. Furthermore, the robustness and efficiency of the developed inverter control platform, encompassing both hardware and software elements, are highlighted. This emphasis on a well-engineered control system not only ensures seamless operation but also underscores the inverter's reliability, vital in the demanding realm of heavy-duty electric transport.
Through rigorous validation and analysis, the report not only confirms the hybrid inverter design's adherence to performance criteria but also forecasts its potential applicability in real-world scenarios and serves to guide future research in power converter technology and its integration into sustainable transportation solutions.