Fault-tolerant control (FTC) is a strategy that aims to keep closed-loop systems stable when components, sensors or actuators fail, maintaining predefined specific performance requirements, and increasing the resilience of the system against failures.
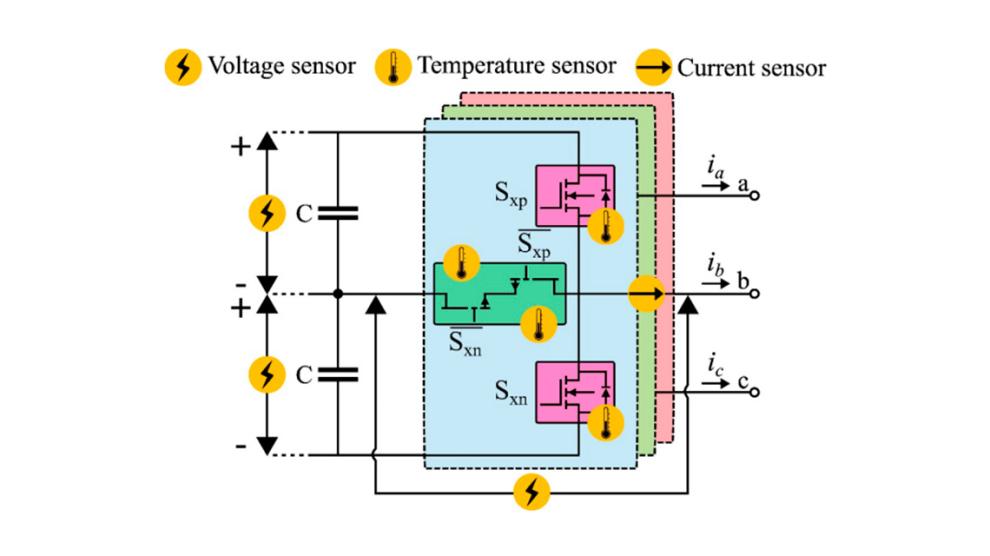
In the RHODAS project, the objective is to design a new high voltage and high power (150kW rated, 250 kW maximum) power inverter that can be integrated with an electric motor of at least 650Vrms phase to phase, coupling to a gearbox system. In this system, if a critical fault occurs (short circuit, overvoltage, etc.) the protections at the converter level will act, stopping the operation of the drive.
However, harsh drive operating conditions, mechanical wear, aging components, or suboptimal manufacturing processes can lead to failures. Initially inconspicuous, these failures may progress in severity over time, ultimately leading to the breakdown of other crucial components. In extreme cases, a sudden serious failure can render electric vehicle systems inoperative, posing substantial safety risks. Consequently, it becomes imperative to implement a fault diagnosis system tailored to the diverse operating modes of the powertrain. This diagnostic mechanism must adeptly identify various potential faults, ensuring the safety of both the driver and the electric vehicle. Upon successful diagnosis, the implementation of a fault-tolerant control strategy becomes essential. This strategy aims to mitigate the impact on the vehicle's usability and elevate operating safety levels in the face of non-critical failures.
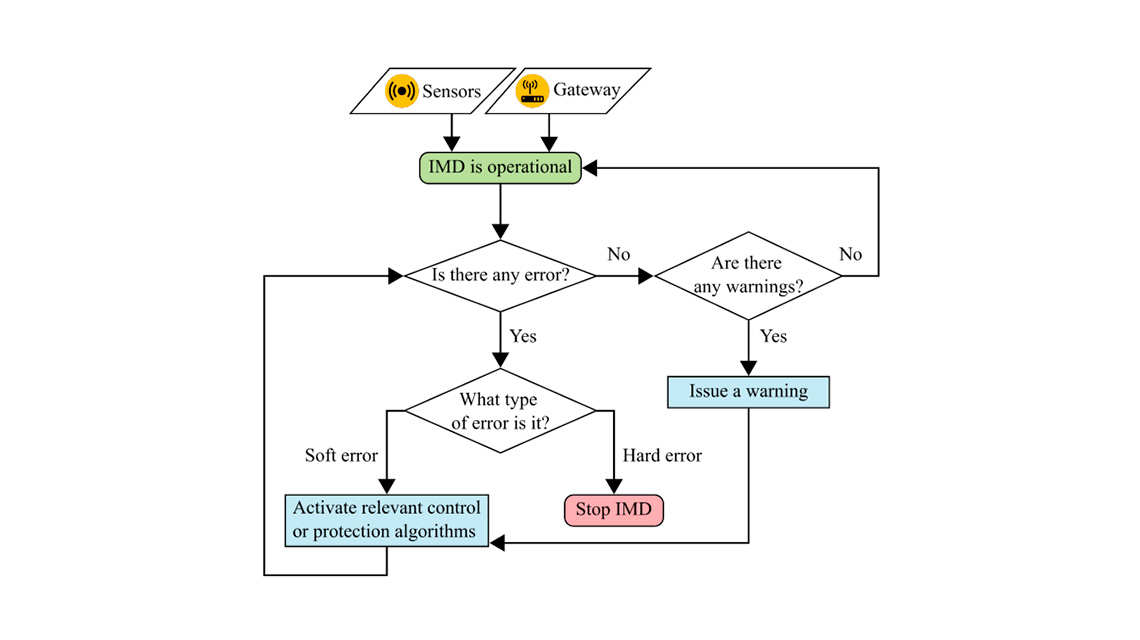
A new report by UNIVERSITAT POLITÈCNICA DE CATALUNYA delves into the fault-tolerant control system for the SiC-GaN T-type hybrid converter developed within the RHODaS project. Initially, the concept of fault-tolerant control is introduced along with the different control levels within the proposed integrated motor drive (IMD). Various failure scenarios that may occur in the power converter are addressed, providing detailed insights into their root causes and potential impacts on the system. Additionally, preventive strategies are discussed, emphasising key parameters that demand continuous monitoring to mitigate potential issues. The report also conducts a detailed analysis of the sensors integrated into the system, elucidating the functions that will be implemented based upon the data acquired by these sensors.
Overall, the report provides a thorough insight into the fault detection, localisation, and mitigation algorithms intended for implementation in the power converters and the IMD system. These algorithms aim to efficiently identify, locate, and mitigate anomalies, enabling a swift and effective response to critical situations. Other key outcomes were the defining of fault-tolerant control concepts, detailing potential faults in the converter and motor, and examining sensor functionalities.
The report will be updated in September 2024, coinciding with the advancement of the high-power converter design and the completion of testing for fault detection, localisation, and mitigation algorithms.
Download and read the full report here D4.1 FAULT TOLERANT CONTROL OF SICGAN POWER CONVERTERS
Image 1: Scheme of a low-power converter module with its respective sensors
Image 2: Flowchart of the proposed fault tolerance algorithm