In this article, we are going to discover more on the topic of ecodesign and the approach that has been taken in the RHODaS project.
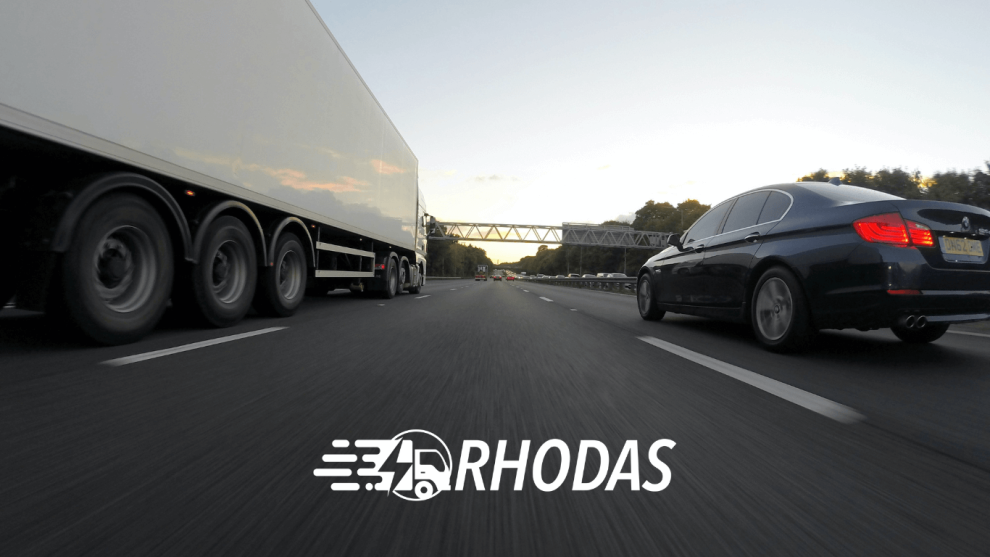
What is ecodesign?
According to the EEA, ecodesign is the integration of environmental aspects into the product development process, by balancing ecological and economic requirements and striving for products which make the lowest possible environmental impact throughout the product life cycle. Applied to the automotive sector, ecodesign (which includes waste prevention and reuse) can bring net savings to businesses while reducing total annual greenhouse gas emissions. That is a win-win situation, but what does it imply to address ecodesign considerations while developing new products?
Adding ecodesign in the development of more efficient powertrains
Despite their technical advantages, modern electric powertrains, in particular their converters and motor controllers, unfortunately contain critical raw materials (CRMs), such as Gallium and Silicon, used in new semiconductor wide band gap (WBG) materials and might be questionable from an environmental perspective. The powertrains are manufactured with emitting emissions like CO2. In the use the powertrain needs electricity and, at end of life, the powertrain needs to be repaired, remanufactured or recycled. Along the whole product life cycle, environmental impacts occur and they have to be taken into account when developing a product. The ecodesign approach supports the whole powertrain development process through environmental, circularity, and criticality assessments and ecodesign considerations.
The guiding questions are what the overall contribution of the powertrain to the material’s criticality is, what the environmental impacts are in each lifecycle stage, and which design recommendations can be made to reduce the impacts. How circular is the product in general right now and which circularity considerations can be adapted to improve the powertrain’s environmental performance?
In this way, the right decisions can be made at any point in time. For the design of powertrains, aspects like material substitution and reduction, technical lifetime, use time, upgradability, durability, modularity etc. must be considered. Realising circular strategies like repair, reuse, remanufacturing and recycling (recover critical materials or components/modules containing critical materials) requires appropriate scenarios and are considered and defined in advance, as they influence the design of the powertrain.
The outcomes of this previous analysis are collected in a guideline with design requirements along environment, criticality and circularity of electrical powertrains with a specific focus on:
- End-of-life and circular strategies to influence the design for separating and recovering the powertrain parts that can be more easily treated, recycled or repaired;
- Definition of relevant circular economy strategies for electric vehicles in general, and specifically for the powertrain and its individual components (drive, converter, control unit, switches, sensors, etc.);
- Derive circular design requirements for each strategy and each group of components;
- Application and integration of the design for separating and recovering the powertrain parts.
Ecodesign in the RHODaS project
Within the project, 30% of the total IMD’s Global Warming Potential (GWP) should be reduced. The integrated motor drive (IMD) powertrain will be analysed on an environmental basis. The Technical University of Vienna (TUW) will guide the project in this direction and will perform several assessments on the environmental burdens, the material criticality and the material circularity.
The assessment results are translated into the Ecodesign Guideline for the RHODaS project in the next step. The Ecodesign Guideline is meant as a supporting method for product development to make decisions towards a more environmentally friendly product. This Ecodesign Guideline also includes elements like material selection matrixes and property charts.
In RHODaS, a highly effective WGB-based power converter design for IMDs is integrated with digital tools in a holistic approach, where ecodesign and circularity concepts are addressed, to create compact and modular solutions that can be integrated into a wide range of heavy-duty vehicles –but also easily applicable to light-duty vehicles enabling these electric vehicles to be more sustainable and autonomous throughout the entire lifecycle of their components.
Impact of the ecodesign in the development of new powertrains
RHODaS will achieve more than a 50% reduction in size and a 30% reduction in weight of the power converter, taking advantage of the application of GaN and hybrid configurations of SiC-GaN to boost performance using the minimum amount of material. Ecodesign principles, together with circular design strategies, will also help in unifying 3D design and manufacture with performance and safety requirements, in order to create cost-efficient integrated IMD approaches. By using simulations prior to the fabrication of the base modules for modular power electronics, it will be easier to assess the potential of dismantling and reusing components and materials.
By including ecodesign approaches, RHODaS aims at promoting an increase in societal awareness and user acceptance of the benefits of the innovative electric powertrain developed and, more in general, of electric heavy-duty vehicles utilisation.
In conclusion, RHODaS represents a step forward to the reduction of transport environmental impacts, and promotes a more sustainable circular economy by supporting the growing demand from consumers for more environmentally friendly technologies and products.
Authors
Philipp Feuchter, Rainer Pamminger, Sebastian Glaser (TUW), Mara Mennella (KNEIA)
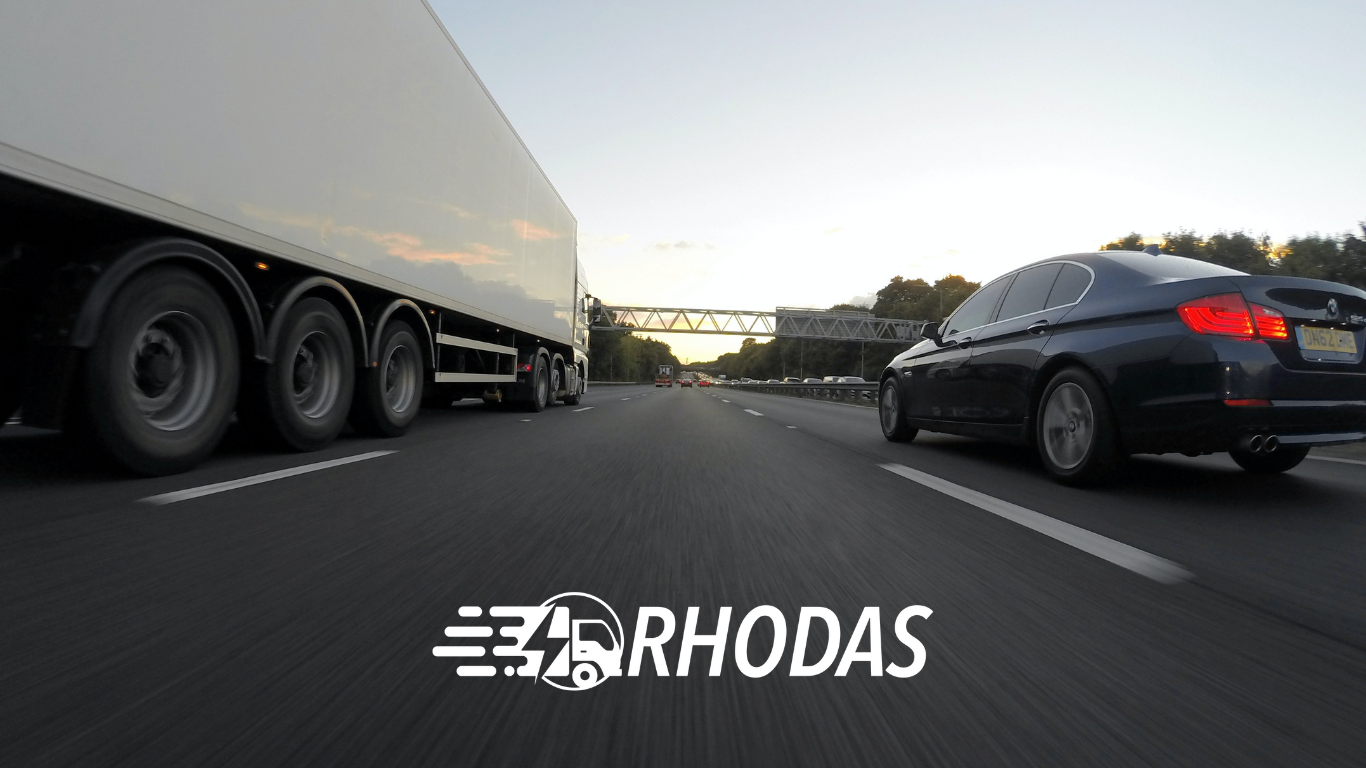