A recent report from the Austrian Institute of Technology entitled "3D Modelling of the DC/DC and DC/AC Converters" presents a comprehensive analysis of the thermal management system for high-performance power converters in heavy-duty electric transport within the RHODaS project.
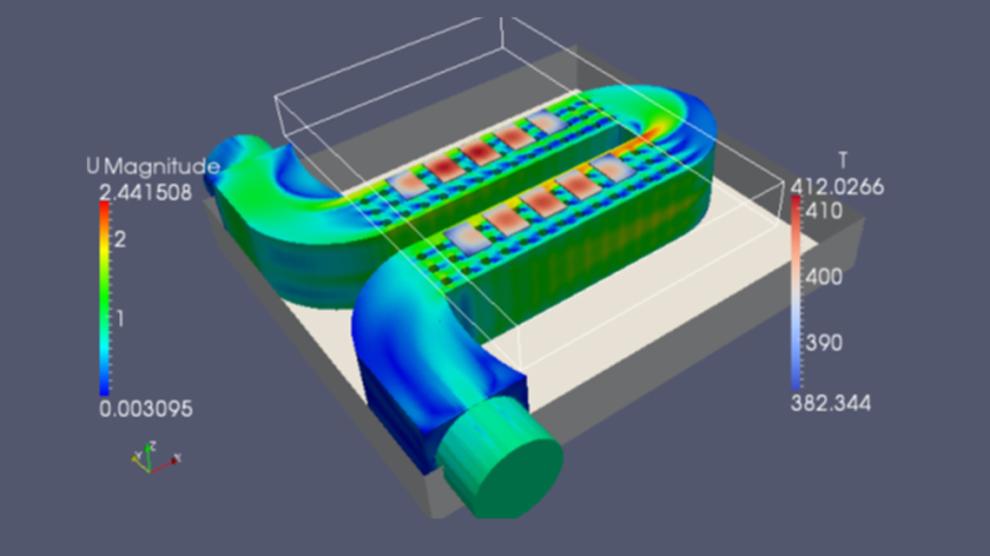
The objective of the research is to optimise the design of the heatsink and investigate the effects of different configurations on heat dissipation. The study focuses on silicon carbide (SiC) and gallium nitride (GaN) semiconductors used in the RHODaS T-type 3-level inverter and outlines the estimation of total losses for heatsink design and provides insights into the advantages and disadvantages of different heatsink concepts.
Initially, an estimation of power losses for SiC and GaN semiconductors based on simulation results was determined, taking into account the varied thermal resistance of the heatsink which then informs the design. Researchers explored different concepts such as functional, geometrical, and mixed designs with each concept being analysed in terms of its advantages, disadvantages, and thermal performance. Computational Fluid Dynamics (CFD) simulations were performed to investigate the thermal characteristics of the heatsink. The simulations consider factors such as fin arrangement, fin height, and heatsink body shape. The effects of these factors on heat dissipation efficiency and temperature distribution were thoroughly examined.

Conclusions from the research indicate that the mixed design concept, which incorporates separate coolant inlets for SiC and GaN modules, provides the best cooling functionality. This design ensures temperature uniformity and allows for individual control of coolant flow to each module; however, it also increases the complexity and cost of the heatsink system. This highlights the importance of optimising fin height and heatsink body shape. It was found that reducing the heatsink height improves heat dissipation and lowers the maximum temperature of the cold plate. Smaller fins also result in better velocity distribution and enhanced heat dissipation efficiency.
Overall, the research into the thermal management of power converters represents a significant step towards the development of high-performance power converters for heavy-duty electric transport. By optimising the design of the heatsink and investigating different configurations, the thermal management system can effectively dissipate heat generated by SiC and GaN semiconductors. The findings of this research can lead to the development of more efficient and cost-effective propulsion systems for electric vehicles. Further studies and advancements in thermal management strategies will be crucial in meeting the increasing power demands of electric transport while ensuring optimal performance and reliability.